Reminder of the project description
Purpose of the project:
Our team of 5 second year engineering students, called DaVinci Industry, is working on the theme of robotics and automation. Indeed, the main objective of this project is to develop a gripper for an industrial robot, in order to reconstitute a module of an industrial production line.
Our robot should be able to move eggs arriving from a conveyor belt and then from a chute to a box. In a second phase, the objective will be to use sensors to allow the robot to adapt and act according to its environment. Eventually, the robot should also be able to place the eggs intelligently in the box.
The egg carton will move on a conveyor belt to the end of the line where it will be emptied by the robot.
Purpose of the project:
Our team of 5 second year engineering students, called DaVinci Industry, is working on the theme of robotics and automation. Indeed, the main objective of this project is to develop a gripper for an industrial robot, in order to reconstitute a module of an industrial production line.
Our robot should be able to move eggs arriving from a conveyor belt and then from a chute to a box. In a second phase, the objective will be to use sensors to allow the robot to adapt and act according to its environment. Eventually, the robot should also be able to place the eggs intelligently in the box.
The egg carton will move on a conveyor belt to the end of the line where it will be emptied by the robot.
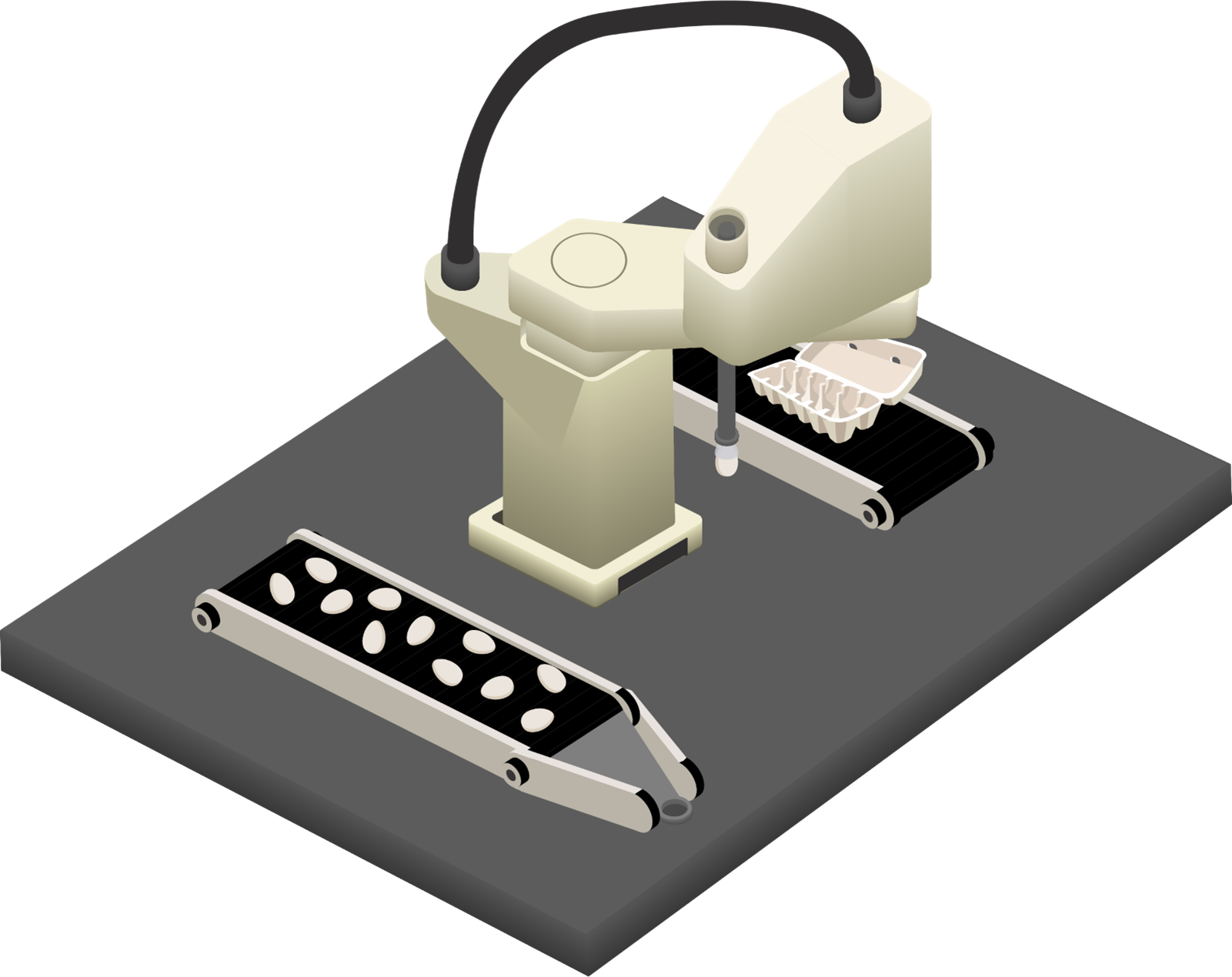
Composition of the team :
Referent: Théophile Jegou du Laz
Other team members: Hugo Bessis, Thomas Culino, Adrien Lefevre, Paul Malaud
Various contributors (association, external industrialists, etc.): Entreprise: Stago.
The project was allowed and carried out under the supervision of Mr Bidault who helped us, advised us and allowed us to order our parts.
Referent: Théophile Jegou du Laz
Other team members: Hugo Bessis, Thomas Culino, Adrien Lefevre, Paul Malaud
Various contributors (association, external industrialists, etc.): Entreprise: Stago.
The project was allowed and carried out under the supervision of Mr Bidault who helped us, advised us and allowed us to order our parts.
Expected and achieved results
Our goal for this project was to develop a reliable, fast and accurate gripper capable of handling objects of various sizes and geometries. The robot had to be able to use this gripper to move objects.
Our goal for this project was to develop a reliable, fast and accurate gripper capable of handling objects of various sizes and geometries. The robot had to be able to use this gripper to move objects.
The first application case for our gripper was to be an egg because the difficulty of gripping this object allows us to test our production. We also had to develop conveyors to move eggs and their boxes around the cage.
We are able to manipulate the robot to make it make movements from a computer or through the teaching box. We assembled a vacuum gripper that allows us to lift and move objects using a vacuum pump system connected to the gripper.
Our final goal was for the robot to be able to control the solenoid valve to trigger a vacuum pump suction into the gripper, as well as control the start of the conveyor.
Our final goal was for the robot to be able to control the solenoid valve to trigger a vacuum pump suction into the gripper, as well as control the start of the conveyor.
This is achieved by an Arduino "joystick" placed on the metal axis of the robot, which is in a pvc tube in which wooden rods are placed. The joystick is fixed on the axis with a 3D printed support. When the axis rotates, the joystick hits one of the sticks and activates the vacuum pump. As the conveyor uses a tubular motor normally used to rotate flaps, we could directly program a distance the flap would travel as it rotated.
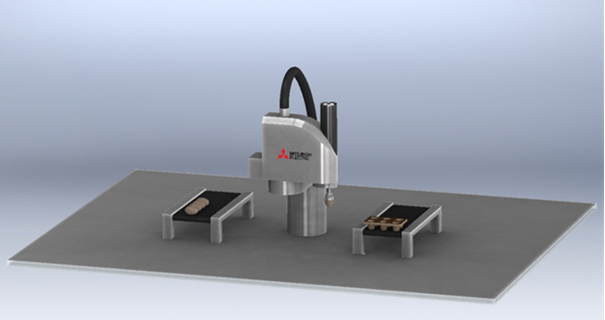
The circuit with the joystick, the Arduino board, to activate or not the solenoid valve has been created and works well but has not been implemented on the robot. A prototype of the conveyor was created with a belt that was made from a recovered flap. We still needed to create a part in SolidWorks to attach the motor to the bracket. We had to fix a cylinder on this axis to make the belt turn.